Capstone 2 Blog 5
- Raphael Luu
- Feb 4, 2024
- 2 min read
Updated: Feb 17, 2024
Since December 11, a significant of materials have been acquired for fabrication. A roll of 60 sqft of stainless steel 304 has been acquired and provided to the machinist for fabrication of the prototype devices. Filament and structural components have also been acquired for the fabrication of the 1:10 scale aircraft. The wings for the aircraft have been completed, however the body is under review to reduce print weight and streamline assembly/disassembly of the aircraft. The team has also met with several different machinists to inquire about machining of the hangers and mechanical components for the prototype device. The machinists from team members’ work locations are still pending on involvement, however the university machinist has collected fabrication materials and is currently providing assistance with part design revisions for ease of machinability. Below are pictures of completed printed parts, including the wings and sample prototype hanger components.

Tasks to be completed by February 17 include finalization of the 1:3 scale bill of materials, acquisition of remaining materials, coding for the linear actuator, and completion of the 1:10 validation aircraft body. In terms of milestones, the team would like to reach halfway through the first milestone of Prototype Devices Fabricated (this milestone has expected completion date of March 2, shown below). Additionally, parts that the university machinist has requested revisions for will be submitted for his approval. Consultation with the other machinists is still ongoing in hopes of streamlining the fabrication process, since the university machinist has confirmed that he will not be able to begin part creation until the week of March 18.

After a second meeting with the university machinist, one of the obstacles presented is not being able to manufacture the hooks that will be utilized for the moving mechanism due to the complex geometries. This component has been redesigned into a much simpler part with the addition of a bracket for support. The images below show the component before and after redesign.


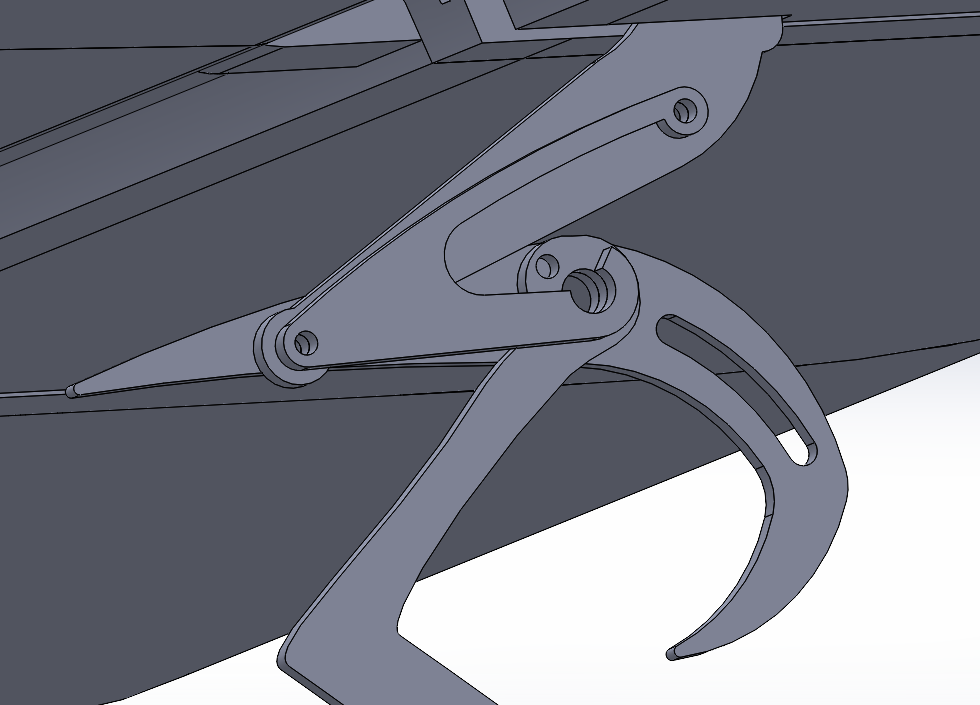
Another obstacle is the fabrication of the 1:10 validation aircraft. The aircraft must be printed in small parts due to the maximum printer size and should ideally be under 2 kg for the current selection of validation equipment. This requires implementing the design of attachment mechanisms to allow for the aircraft to be easily assembled and disassembled (for transportation), while remaining under 2 kg net weight for an estimated 18 sub-parts remaining. Back up plans for this issue include reducing the number of parts that need connectors by gluing together bigger subparts, or increasing budget on equipment to increase max weight. Below are pictures of ongoing assembly designs for the aircraft.


Comments