Capstone 2 Blog 6: Progress Update
- Raphael Luu
- Feb 17, 2024
- 3 min read
During the work period spanning February 4th to February 17th, the team has chosen to employ 3D printing for the mechanical system validation, producing parts at a 1:3 scale to facilitate assembly. This approach ensures that the assembly process closely resembles the anticipated procedure for the manufactured metal pieces scheduled for production in mid-March.
Regarding electronics, significant progress has been made, with most components now completed. Notably, the linear actuator is now controllable via a control switch at various points along the extension length, enhancing its functionality. Minimal changes might be needed to the coding once all the components for the mechanical system are pieced together.

Due to how small the parts are at the 1:10 scale, the machinist has made several requests for minor part edits to reduce the challenge of machinability. This process is currently ongoing, with the most recent meeting with the machinist being the 14th of February followed by requests for thru-hole edits. Below is a picture of past revisions that have been printed and shown to the machinist (the geometry is constant, and edits were to holes, slots and thickness).
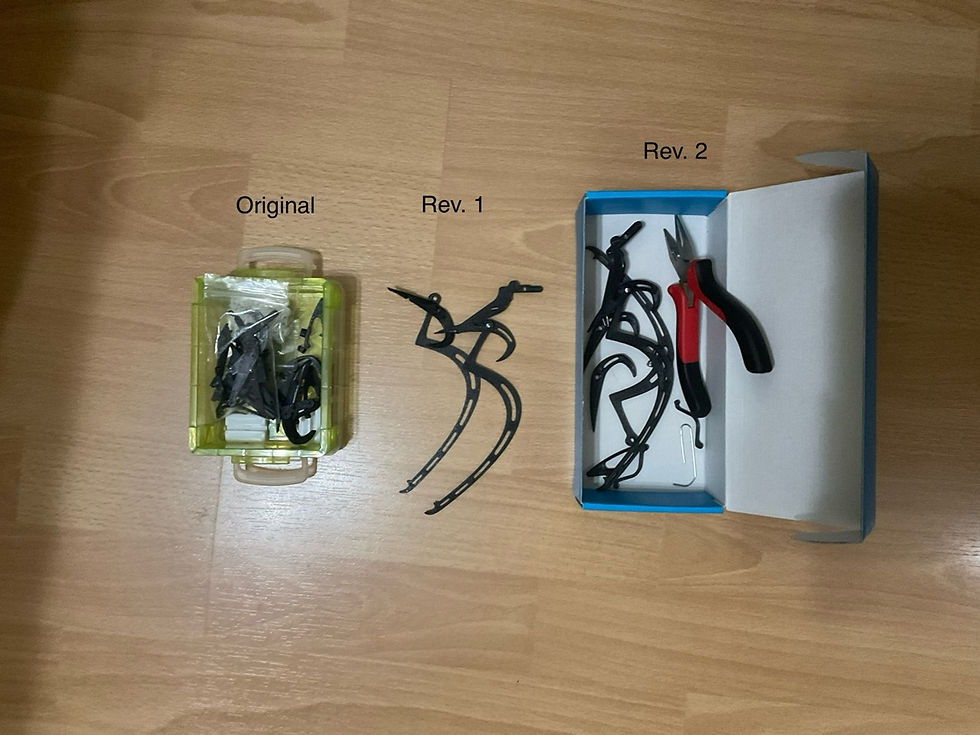
Additionally, an issue regarding 1:10 validation was brought up questioning the need of validating the entire system on a model aircraft with the alternative option of placing a section of the system in the wind tunnel. After reaching out to Professor Love, it was concluded that using the aircraft would yield more meaningful results. A model of this validation set up and its details is in progress and will be provided for instructor approval prior to obtaining testing equipment.
For the next work period until March 9, it is expected to have completed the first milestone completed, excluding the production of machined parts due to the machinist’s schedule. This includes the completion of the validation aircraft and 1:10 scale system, as well as the 1:3 scale prototype. Progress into the second milestone is also anticipated, in which testing setup and equipment will be prepared in order to be ready for validation testing as soon as the machinist completes production of parts. 3D printed parts will be used in place until the machined parts are available.
The challenges of fabricating the 1:10 scale validation aircraft are still persistent, since the prints are close to the maximum bed size and the reduction of weight costs structural integrity. Different cuts along the aircraft are being tested to see which is the best orientation for printing. Back up plans for this issue will include the use of adhesives on smaller prints and an increase in budget for the motor to increase the maximum weight requirement. Shown below is the progress of plane body parts production (shown as assembly due to section cuts still under experiment).
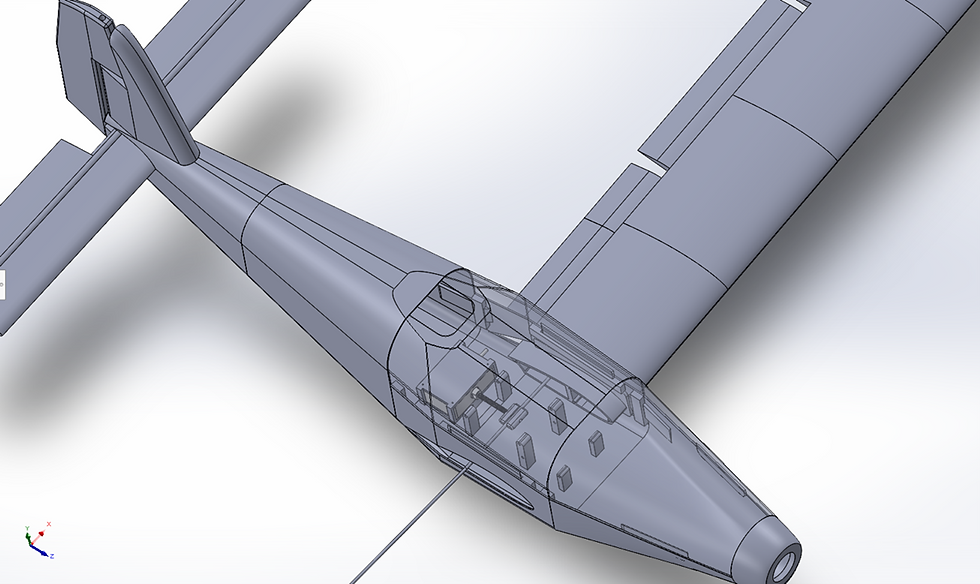
One obstacle for the 1:3 scale validation is figuring out a way to reliably validate that the boom moves the correct horizontal and vertical distance from its starting point. The team also has an obstacle of emulating the drag forces found in the teams 1:10 drag test on our 1:3 scale. For the 1:3 scale validation a potential solution is to have the setup attached to a base that will have another piece of wood protruding from the base that will prevent the boom from moving further than the intended distance and serves to accurately determine whether the boom moved the appropriate amount.
Comentarios